Propiedades del niquelado químico
Dureza y resistencia al desgaste
Dureza
Los recubrimientos NIPLATE® poseen una dureza notablemente superior a la de los sustratos típicamente recubiertos, lo que contribuye a aumentar sus propiedades tribológicas. En comparación con los recubrimientos tradicionales y comercialmente comparables (como el níquel electrolítico, la oxidación anódica del aluminioy los tratamientos termoquímicos de los aceros), manifiestan una dureza media más alta, comparable a la del recubrimiento de cromo duro.
No obstante, cabe señalar que la dureza del níquel químico es inferior a la de los recubrimientos especiales, como el pulverizador de plasmao el PVD/CVD, que sin embargo, presentan notables diferencias en términos de coste y aplicación.
En la siguiente tabla se resumen las durezas de los recubrimientos que se pueden obtener en relación con los tratamientos térmicos realizados:
Dureza [HV] | Deshidrogenación 150-180 °C x 4 h | Endurecimiento 260-280 °C x 8 h | Endurecimiento 330-350 °C x 4 h |
---|---|---|---|
NIPLATE® 500 | 550 ± 50 HV | - | 1000 ± 50 HV |
NIPLATE® 600 | 700 ± 50 HV | 800 ± 50 HV | 1000 ± 50 HV |
NIPLATE® 500 PTFE | 250 ± 100 HV | 300 ± 100 HV | - |
NIPLATE® 600 SiC | 700 ± 50 HV | 850 ± 50 HV | 1050 ± 50 HV |
CONSEJOS PRÁCTICOS
La máxima dureza de los recubrimientos NIPLATE® se puede obtener mediante un tratamiento de endurecimiento a 340 °C durante 4 horas. Este proceso provoca una coloración amarilla-azul iridiscente del recubrimiento. Si es necesario, es posible realizar un tratamiento térmico de endurecimiento en una atmósfera inerte. Este método permite alcanzar la máxima dureza del recubrimiento, manteniendo inalterada la coloración blanca metálica del níquel químico.
Resistencia al desgaste
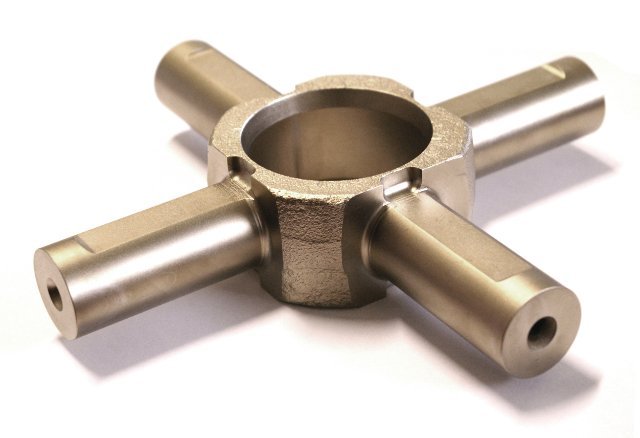
Gracias a su dureza y cohesión, los recubrimientos NIPLATE®, en particular el NIPLATE® 600 y el NIPLATE® 600 SiC, permiten obtener una elevada resistencia al desgaste de las superficies tratadas.
El NIPLATE® 600, con un contenido del 7 % de fósforo en aleación, ofrece una alta resistencia al desgaste abrasivo, al desgaste adhesivo y al «fretting», tanto en ambiente lubricado como en seco. La dureza alcanzada con los tratamientos térmicos de endurecimiento y los altos espesores de recubrimiento que se pueden obtener (hasta 50-70 µm) permiten aumentar la vida útil del componente y obtener una resistencia al desgaste similar a la del cromo duro, con la ventaja de no tener que rectificar posteriormente la pieza y tener un espesor de recubrimiento uniforme en toda la superficie, tanto interna como externa.
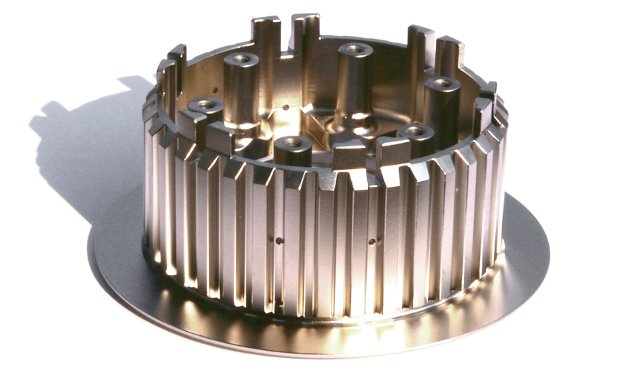
Para aplicaciones críticas, donde el desgaste del componente es máximo, se ha estudiado el NIPLATE® 600 SiC, recubrimiento compuesto de matriz NIPLATE® 600 que contiene granos microcristalinos de carburo de silicio en una cantidad del 20-30 % en volumen. Las partículas de carburo de silicio, material cerámico sintético ultra duro, permiten obtener un recubrimiento con características de resistencia al desgaste extraordinarias. La resistencia al desgaste abrasivo del NIPLATE® 600 SiC es hasta 10 veces mayor que la del cromo duro. Este recubrimiento se utiliza en sectores altamente tecnológicos —como en competiciones automovilísticas— para aumentar el rendimiento sin disminuir la vida útil de los componentes, así como en el sector textil para proteger los componentes sujetos al desgaste constante del hilo empleado para tejer.
CONSEJOS PRÁCTICOS
- Para componentes sujetos a un fuerte desgaste, prever un espesor de tratamiento de al menos 20 µm y un posterior tratamiento de endurecimiento a 280 °C durante 8 horas o, mejor aún, a 340 °C durante 4 horas.
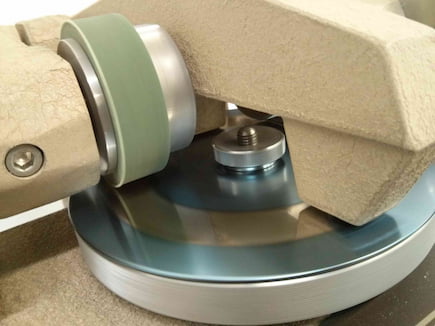
Prueba de desgaste abrasivo Taber Abraser
El test más utilizado para la medición de la resistencia al desgaste abrasivo en los recubrimientos es el Taber Abraser Test. La prueba de desgaste en los recubrimientos de níquel químico está especificada por la normativa estadounidense ASTM B733. Los parámetros de prueba son los siguientes:
- Ruedas abrasivas: CS-10
- Carga en una sola rueda: 1000 g
- Altura boquillas aspiración: 1 mm
La prueba se realiza montando las probetas sobre un plato giratorio en el que son sometidas al contacto de dos ruedas abrasivas que ruedan y al mismo tiempo se arrastran, bajo la aplicación de una fuerza específica. Los residuos de desgaste durante la prueba son aspirados por medio de dos boquillas situadas sobre la probeta. Al final de la prueba de desgaste se calcula el Taber Wear Index (TWI), índice del desgaste sufrido por el recubrimiento, calculado como variación media del peso expresada en mg por cada 1000 ciclos.
En la siguiente tabla se muestran los valores de TWI de los recubrimientos NIPLATE®. Un valor bajo indica una mayor resistencia al desgaste abrasivo.
Resistencia al desgaste [TWI] | Deshidrogenación 150-180 °C x 4 h | Endurecimiento 260-280 °C x 8 h | Endurecimiento 330-350 °C x 4 h |
---|---|---|---|
NIPLATE® 500 | 20 TWI | - | 10 TWI |
NIPLATE® 600 | 16 TWI | 12 TWI | 9 TWI |
NIPLATE® 500 PTFE | 33 TWI | 19 TWI | - |
NIPLATE® 600 SiC | 0,70 TWI | 0,65 TWI | 0,60 TWI |