Propiedades del niquelado químico
Resistencia a la corrosión
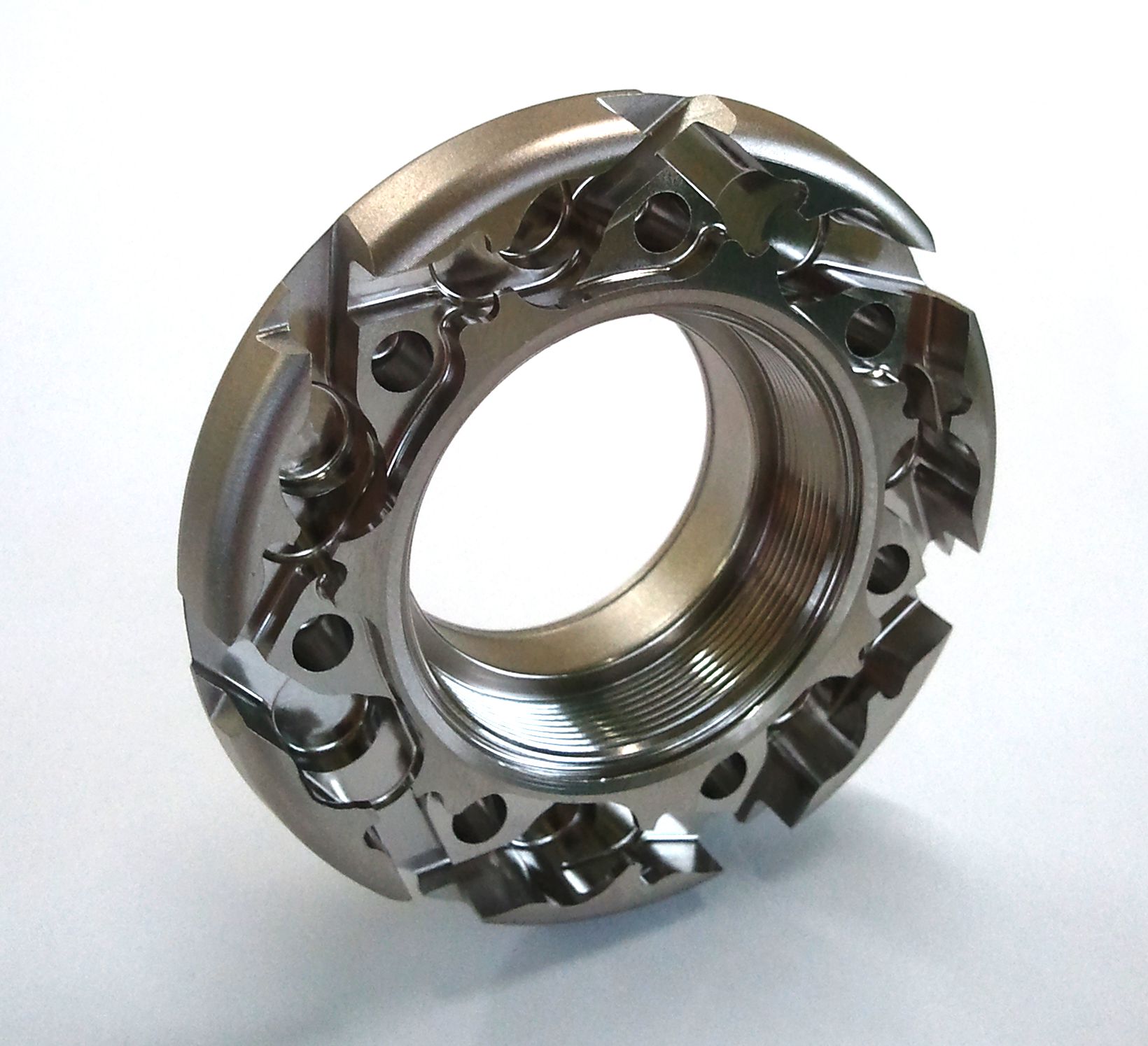
Una de las características más destacadas de los recubrimientos NIPLATE® es su resistencia a la corrosión. Estos recubrimientos están compuestos por una aleación de níquel y fósforo, y presentan una elevada resistencia química en ambientes típicamente agresivos hacia las aleaciones metálicas comunes, como atmósferas marinas, industriales y entornos viales. Además, los recubrimientos Niplate no son susceptibles al ataque químico de hidrocarburos y disolventes.
Mecanismo de protección
El mecanismo de protección a la corrosión de los recubrimientos NIPLATE® se realiza mediante el aislamiento del material base del ambiente corrosivo. Gracias a su uniformidad en toda la superficie de la pieza, protegen contra la corrosión incluso geometrías complejas.
La resistencia a la corrosión mejora con el aumento del espesor del NIPLATE®, reduciendo la porosidad intrínseca del recubrimiento. Sin embargo, en la superficie pueden existir puntos de discontinuidad, debido a diferentes causas, como porosidad gruesa del material base, inclusiones no metálicas en la aleación, grietas en el recubrimiento o daños debidos a la manipulación o procesamiento mecánico. Esto puede exponer el metal base a la acción agresiva del entorno exterior, provocando puntos de corrosión.
Los recubrimientos de níquel químico de alto contenido en fósforo NIPLATE® 500 y NIPLATE® eXtreme presentan una porosidad muy baja incluso con espesores finos. Por lo general, con un espesor superior a 30 µm, estos recubrimientos presentan una porosidad nula.
Protección de las aleaciones de cobre
Para las aleaciones de cobre, el mecanismo de protección es diferente. El cobre tiene un potencial de oxidación-reducción mayor que el níquel, por lo que el recubrimiento de níquel químico también crea una protección catódica del material base. Esto se traduce en una resistencia excepcional a la corrosión de las aleaciones de cobre recubiertas con NIPLATE®, incluso en presencia de posibles daños y discontinuidades del recubrimiento.
Esto hace que las aleaciones de cobre tratadas con recubrimientos de niquelado químico se puedan utilizar en ambientes marinos incluso en presencia de contacto directo entre el agua de mar y las piezas tratadas.
CONSEJOS PRÁCTICOS
- Aleaciones de cobre: son el material base que está mejor protegido contra la corrosión a través de los recubrimientos NIPLATE®.
- Aleaciones de aluminio o acero al carbono: para aplicaciones en las que la resistencia a la corrosión es fundamental, se debe prever un espesor de recubrimiento de al menos 20 µm en aleaciones de aluminio o acero al carbono.
- Calidad y procesamiento mecánico: para maximizar la resistencia a la corrosión, se recomienda utilizar una materia prima de alta calidad, sin porosidad ni inclusiones. También es necesario realizar un procesamiento mecánico fino con baja rugosidad, eliminar cualquier rebaba o borde vivo y, en el caso de uso de aceites no emulsionables durante el procesamiento mecánico, realizar un lavado con disolvente de las piezas inmediatamente después del procesamiento.
Prueba de resistencia a la corrosión acelerada en niebla salina neutra
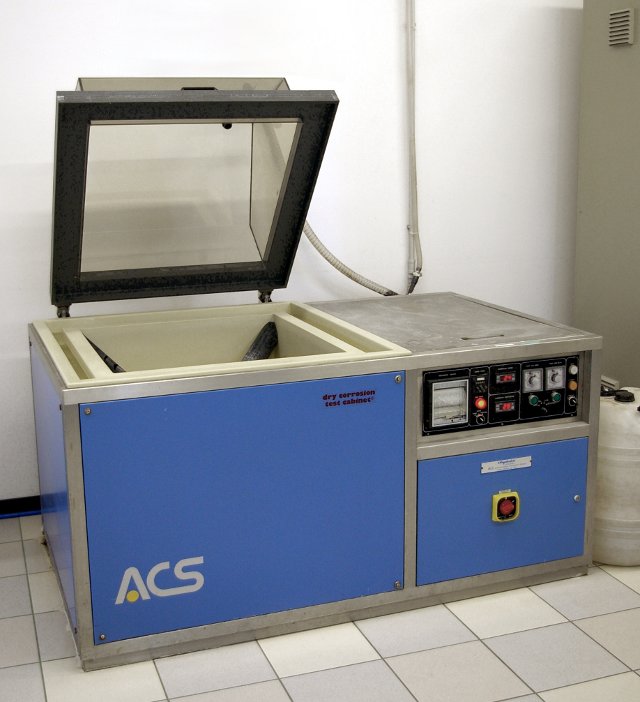
La prueba de resistencia a la corrosión más utilizada en la industria mecánica es la prueba de resistencia a la corrosión acelerada en niebla salina neutra ISO 9227.
Consiste en la exposición de la pieza a una niebla de agua y sal (cloruro de sodio al 5 %) a una temperatura de 35 °C durante un tiempo que suele variar entre 96 y 480 horas, creando un ambiente extremadamente corrosivo para muchos materiales.
Un paso fundamental para la evaluación y definición de la resistencia es la medición del área corroída. A través de esta medida se calcula la calificación de protección Rp según la norma ISO 10289.
Los recubrimientos NIPLATE®
Los recubrimientos NIPLATE® ofrecen una elevada resistencia química a este ambiente corrosivo y son casi completamente inmunes a la corrosión. La protección contra la corrosión se realiza mediante el aislamiento del material base del ambiente; por lo tanto, cualquier discontinuidad del recubrimiento se convierte en una zona potencial de ataque.
Resistencia a la corrosión de aleaciones de hierro y aluminio
La resistencia a la corrosión en niebla salina de las aleaciones de hierro y aluminio recubiertas depende del recubrimiento, del procesamiento mecánico y del material base de la pieza. Teniendo en cuenta los numerosos parámetros involucrados, una definición de la resistencia a la corrosión requiere necesariamente la realización de la prueba de niebla salina en la pieza recubierta.
Resistencia a la corrosión de aleaciones de cobre
El comportamiento en el test de corrosión en niebla salina de las aleaciones de cobre recubiertas con NIPLATE® es diferente. Gracias a la afinidad electroquímica entre el níquel y el cobre, la protección contra la corrosión es notable incluso con espesores de recubrimiento bajos. Una pieza de latón recubierta con 30 µm de NIPLATE® 500 presenta una resistencia a la corrosión en niebla salina, con calificación Rp 9, incluso para una exposición superior a 1000 horas.
Conclusiones
Estas propiedades hacen que los recubrimientos sean NIPLATE® especialmente adecuados para una amplia gama de aplicaciones industriales. La resistencia a la corrosión, determinada a través del test de niebla salina, contribuye significativamente a la extensión de la vida útil de los componentes, asegurando una barrera eficaz contra los agentes corrosivos. Las especificaciones técnicas y las modalidades de aplicación de los recubrimientos NIPLATE® deben verificarse siempre con pruebas en situaciones reales de aplicación, teniendo en cuenta la complejidad y la variedad de las condiciones operativas.