Propriétés du nickelage chimique
Dureté et résistance à l’usure
Dureté
Les revêtements NIPLATE® ont une dureté nettement supérieure à celle des substrats généralement recouverts, ce qui contribue à accroître leurs propriétés tribologiques. Par rapport aux revêtements traditionnels et commercialement comparables (tels que le nickel électrolytique, l’ oxydation anodique de l’alumineet les traitements thermochimiques des aciers), ils présentent une dureté moyenne plus élevée, comparable à celle du revêtement en chrome dur.
Cependant, il convient de noter que la dureté du nickel chimique est inférieure à celle des revêtements spéciaux, tels que le plasma spray, le PVD/CVD, qui, cependant, présentent des différences considérables en termes de coût et d’application.
Le tableau ci-dessous résume les duretés des revêtements qui peuvent être obtenues par rapport aux traitements thermiques effectués :
Dureté [HV] | Déshydrogénation 150-180 °C x 4 h | Durcissement 260-280 °C x 8 h | Durcissement 330-350 °C x 4 h |
---|---|---|---|
NIPLATE® 500 | 550 ± 50 HV | - | 1000 ± 50 HV |
NIPLATE® 600 | 700 ± 50 HV | 800 ± 50 HV | 1000 ± 50 HV |
NIPLATE® 500 PTFE | 250 ± 100 HV | 300 ± 100 HV | - |
NIPLATE® 600 SiC | 700 ± 50 HV | 850 ± 50 HV | 1050 ± 50 HV |
CONSEILS PRATIQUES
La dureté maximale des revêtements peut être NIPLATE® obtenue grâce à un traitement de durcissement à 340 °C pendant 4 heures. Ce processus provoque une coloration jaune-bleu irisée du revêtement. Si nécessaire, il est possible d’effectuer un traitement thermique de durcissement sous atmosphère inerte. Cette méthode permet d’atteindre une dureté maximale du revêtement, en maintenant inchangée la coloration blanche métallique du nickel chimique.
Résistance à l’usure
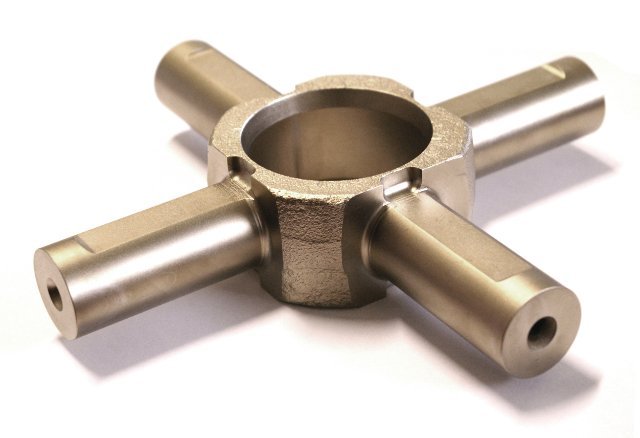
Grâce à leur dureté et à leur cohésion, les revêtements NIPLATE®, en particulier les NIPLATE® 600 et NIPLATE® 600 SiC, permettent d’obtenir une grande résistance à l’usure des surfaces traitées.
Le NIPLATE® 600, avec une teneur en phosphore de 7 % en alliage, offre une résistance élevée à l’usure abrasive, à l’usure adhésive et au frottement, à la fois dans un environnement lubrifié et à sec. La dureté obtenue avec les traitements thermiques de durcissement et les épaisseurs de revêtement élevées pouvant être obtenues (jusqu’à 50-70 µm) permettent d’augmenter la durée de vie du composant et d’obtenir une résistance à l’usure similaire au chrome dur, avec l’avantage de ne pas avoir à rectifier ultérieurement la pièce et d’avoir une épaisseur de revêtement uniforme sur toute la surface, intérieure et extérieure.
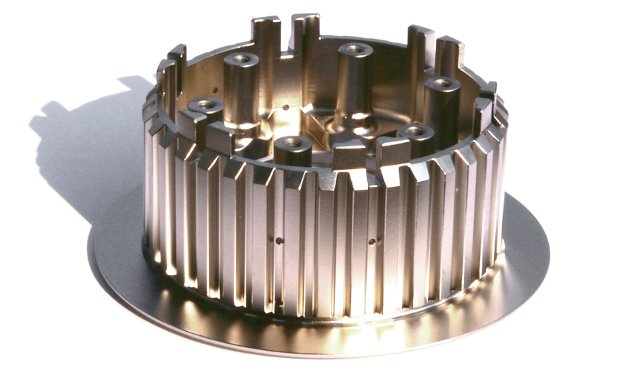
Pour les applications critiques, où l’usure du composant est maximale, le NIPLATE® 600 SiC, un revêtement composite à matrice NIPLATE® 600 contenant des grains microcristallins de carbure de silicium en quantité de 20-30 % en volume, a été étudié. Les particules de carbure de silicium, un matériau céramique synthétique ultra-dur, permettent d’obtenir un revêtement avec des caractéristiques extraordinaires de résistance à l’usure. La résistance à l’usure abrasive du NIPLATE® 600 SiC est jusqu’à 10 fois supérieure à celle du chrome dur. Ce revêtement est utilisé dans les secteurs hautement technologiques, par exemple dans la course pour augmenter les performances sans diminuer la durée de vie des composants, ou dans le textile pour protéger les composants soumis à l’usure constante du fil de tissage.
CONSEILS PRATIQUES
- Pour les composants soumis à une forte usure, prévoir une épaisseur de traitement d’au moins 20 µm et un traitement de durcissement ultérieur à 280 °C pendant 8 heures ou mieux encore à 340 °C pendant 4 heures.
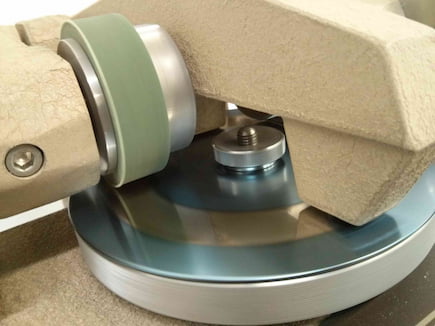
Test d’usure abrasive Taber Abraser
Le test le plus utilisé pour la mesure de la résistance à l’usure abrasive sur les revêtements est le Taber Abraser Test. Le test d’usure sur les revêtements de nickel chimique est spécifié par la réglementation américaine ASTM B733. Les paramètres de test sont les suivants :
- Roues abrasives : CS-10
- Charge sur une seule roue : 1000 g
- Hauteur des buses d’aspiration : 1 mm
Le test est effectué en plaçant les éprouvettes sur une plaque rotative, en les soumettant au contact de deux roues abrasives qui roulent et rampent simultanément, sous l’application d’une force spécifique. Les résidus d’usure pendant l’essai sont aspirés au moyen de deux buses placées au-dessus de l’éprouvette. À la fin du test d’usure, on calcule le Taber Wear Index (TWI), indice d’usure subi par le revêtement, calculé comme une variation moyenne du poids exprimée en mg sur 1000 cycles.
Le tableau suivant indique les valeurs de TWI des revêtements NIPLATE®. Une faible valeur indique une résistance à l’usure abrasive plus élevée.
Résistance à l’usure [TWI] | Déshydrogénation - 150-180 °C x 4 h | Durcissement - 260-280 °C x 8 h | Durcissement - 330-350 °C x 4 h |
---|---|---|---|
NIPLATE® 500 | 20 TWI | - | 10 TWI |
NIPLATE® 600 | 16 TWI | 12 TWI | 9 TWI |
NIPLATE® 500 PTFE | 33 TWI | 19 TWI | - |
NIPLATE® 600 SiC | 0,70 TWI | 0,65 TWI | 0,60 TWI |