Propriétés du nickelage chimique
Résistance à la corrosion
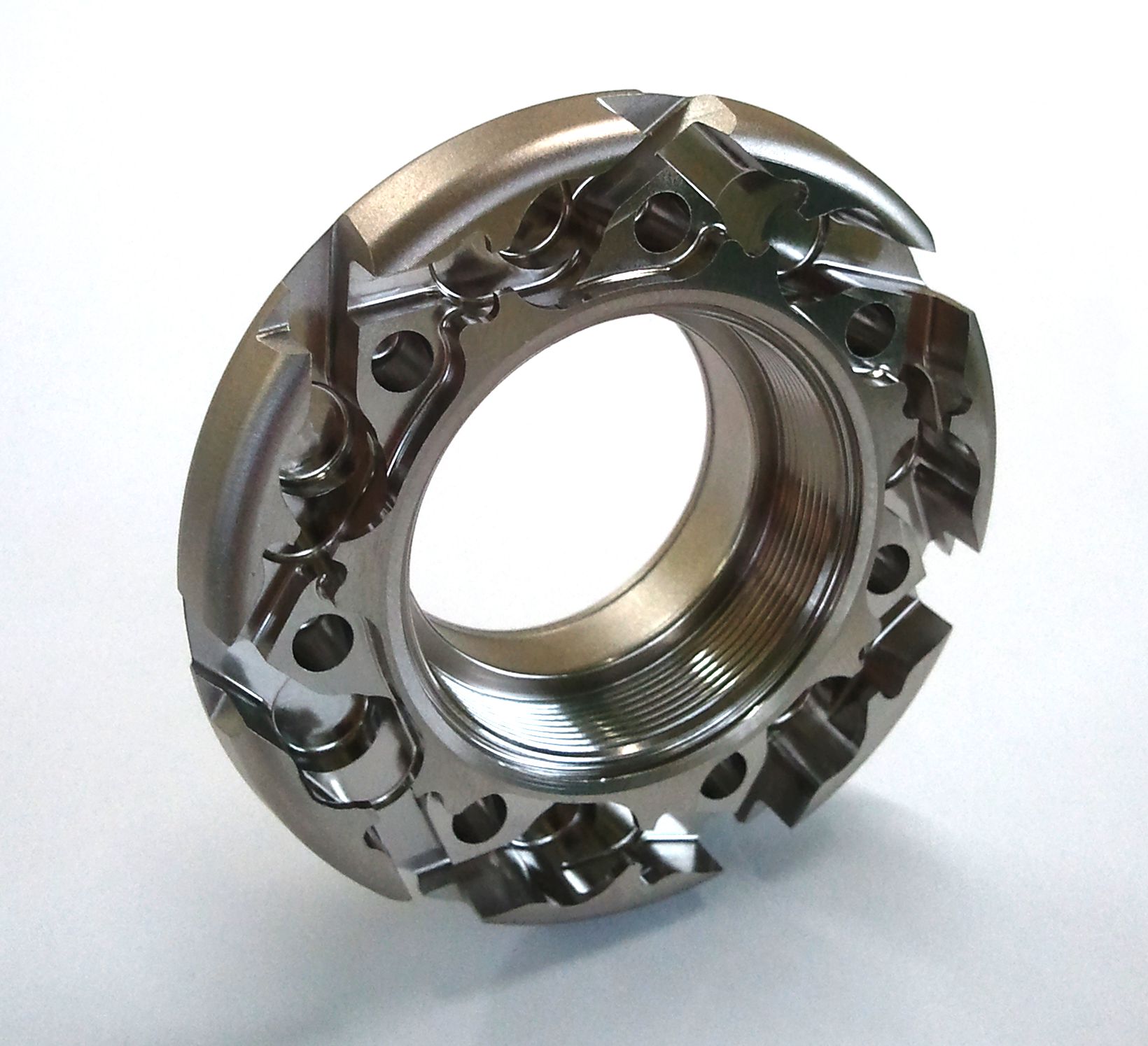
L’une des principales caractéristiques des revêtements NIPLATE® est leur résistance à la corrosion. Ces revêtements sont composés d’un alliage de nickel et de phosphore, présentant une résistance chimique élevée dans des environnements généralement agressifs envers les alliages métalliques communs, tels que les atmosphères marines, industrielles et les environnements routiers. De plus, les revêtements Niplate ne sont pas sensibles aux attaques chimiques par les hydrocarbures et les solvants.
Mécanisme de protection
Le mécanisme de protection à la corrosion des revêtements NIPLATE® se fait en isolant le matériau de base de l’environnement corrosif. Grâce à leur uniformité sur toute la surface de la pièce, ils protègent également les géométries complexesde la corrosion.
La résistance à la corrosion s’améliore avec l’augmentation de l’épaisseur du NIPLATE®, ce qui réduit la porosité intrinsèque du revêtement. Cependant, des points de discontinuité peuvent exister sur la surface, dus à différentes causes telles que la porosité grossière du matériau de base, les inclusions non métalliques dans l’alliage, les fissures du revêtement, ou les dommages dus à la manipulation ou à l’usinage mécanique. Cela peut exposer le métal de base à l’action agressive de l’environnement extérieur, déclenchant des points de corrosion.
Les revêtements en nickel chimique haut phosphore NIPLATE® 500 et NIPLATE® eXtreme, présentent une porosité très faible même à faible épaisseur. Habituellement, avec une épaisseur supérieure à 30 µm, ces revêtements présentent une porosité nulle.
Protection des alliages de cuivre
Pour les alliages de cuivre, le mécanisme de protection est différent. Le cuivre a un potentiel d’oxydo-réduction plus élevé que le nickel, de sorte que le revêtement de nickel chimique crée également une protection cathodique du matériau de base. Cela se traduit par une résistance exceptionnelle à la corrosion des alliages de cuivre recouverts de NIPLATE®, même en présence d’éventuels dommages et discontinuités du revêtement.
Cela signifie que les alliages de cuivre traités avec des revêtements de nickelage chimique peuvent être utilisés dans les environnements marins, même en présence d’un contact direct entre l’eau de mer et les pièces traitées.
CONSEILS PRATIQUES
- Alliages de cuivre : Ce sont les matériaux de base qui sont mieux protégés de la corrosion à travers les revêtements NIPLATE®.
- Alliages d’aluminium ou d’acier au carbone : Pour les applications où la résistance à la corrosion est essentielle, il convient de prévoir une épaisseur de revêtement d’au moins 20 µm sur les alliages d’aluminium ou d’acier au carbone.
- Qualité et usinage mécanique : Pour maximiser la résistance à la corrosion, il est conseillé d’utiliser un matériau brut de haute qualité, sans porosité ni inclusions. Il est également nécessaire d’effectuer un usinage mécanique fin avec une faible rugosité, d’éliminer toute bavure ou arête vive et, en cas d’utilisation d’huiles non émulsionnables pendant l’usinage mécanique, d’effectuer un lavage au solvant des pièces immédiatement après l’usinage.
Test de résistance à la corrosion accélérée en brouillard salin neutre
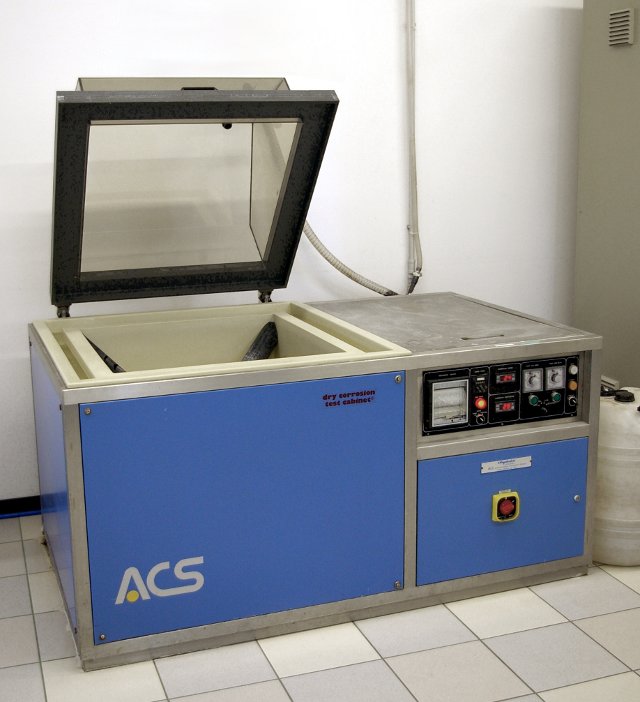
Le test de résistance à la corrosion le plus couramment utilisé dans l’industrie mécanique est le test de résistance à la corrosion accélérée en brouillard salin neutre ISO 9227.
Il implique l’exposition de la pièce à un brouillard d’eau et de sel (chlorure de sodium à 5 %) à une température de 35 °C pendant un temps variable généralement entre 96 et 480 heures, créant un environnement extrêmement corrosif pour de nombreux matériaux.
Une étape fondamentale pour l’évaluation et la définition de la résistance est la mesure de la zone corrodée. Grâce à cette mesure, la note de protection Rp est calculée conformément à la norme ISO 10289.
Les revêtements NIPLATE®
Les revêtements NIPLATE® offrent une résistance chimique élevée à cet environnement corrosif et sont presque complètement immunisés à la corrosion. La protection contre la corrosion se fait par l’isolation du matériau de base de l’environnement ; par conséquent, toute discontinuité du revêtement devient une zone d’attaque potentielle.
Résistance à la corrosion des alliages de fer et d’aluminium
La résistance à la corrosion au brouillard salin des alliages de fer et d’aluminium recouverts dépend du revêtement, de l’usinage mécanique et du matériau de base de la pièce. Compte tenu des nombreux paramètres impliqués, une définition de la résistance à la corrosion nécessite nécessairement l’exécution du test en brouillard salin sur la pièce recouverte.
Résistance à la corrosion des alliages de cuivre
Le comportement au test de corrosion en brouillard salin des alliages de cuivre recouverts de cuivre NIPLATE® est différent. Grâce à l’affinité électrochimique entre le nickel et le cuivre, la protection contre la corrosion est remarquable, même avec de faibles épaisseurs de revêtement. Un morceau de laiton recouvert de 30 µm de NIPLATE® 500 présente une résistance à la corrosion en brouillard salin, avec une note Rp 9, même pour une exposition supérieure à 1000 heures.
Conclusions
Ces propriétés rendent les revêtements NIPLATE® particulièrement adaptés à une large gamme d’applications industrielles. La résistance à la corrosion, déterminée par le test en brouillard salin, contribue de manière significative à la prolongation de la durée de vie des composants, assurant une barrière efficace contre les agents corrosifs. Les spécifications techniques et les modalités d’application des revêtements NIPLATE® doivent toujours être vérifiées par des tests sur le terrain, en tenant compte de la complexité et de la variété des conditions de fonctionnement.