Eigenschaften der chemischen Vernickelung
Korrosionsbeständigkeit
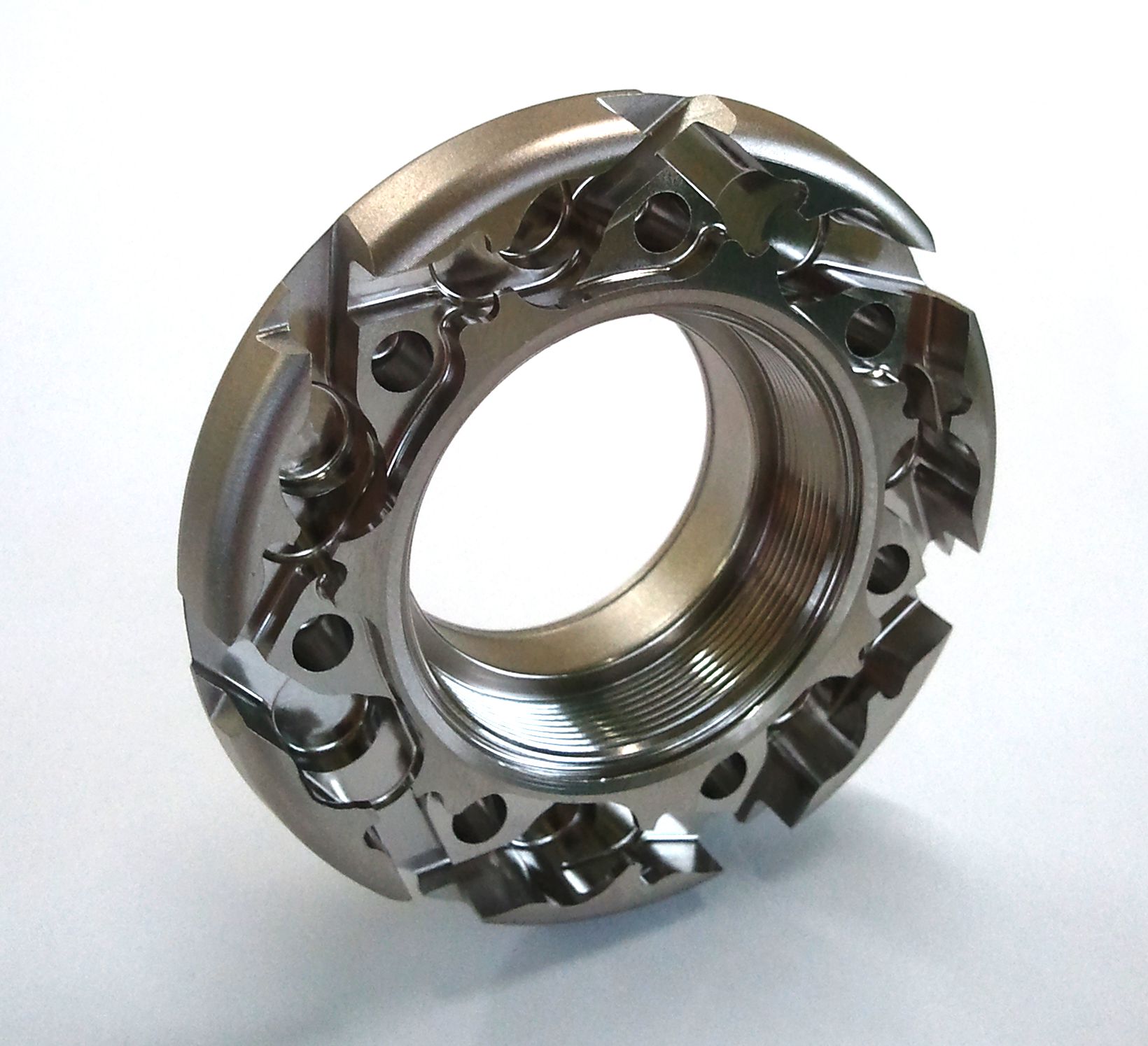
Eines der herausragenden Merkmale der NIPLATE® Beschichtungen ist ihre Korrosionsbeständigkeit. Diese Beschichtungen bestehen aus einer Nickel-Phosphor-Legierung und weisen eine hohe chemische Beständigkeit in Umgebungen auf, die typisch aggressiv gegenüber gängigen Metalllegierungen sind, z. B. in Meeres-, Industrie- und Straßenumgebungen. Darüber hinaus sind Niplate Beschichtungen nicht anfällig für chemische Angriffe durch Kohlenwasserstoffe und Lösungsmittel.
Schutzmechanismus
Der Korrosionsschutzmechanismus der NIPLATE® Beschichtungen erfolgt durch Isolierung des Grundmaterials von der korrosiven Umgebung. Dank ihrer Gleichmäßigkeit auf der gesamten Oberfläche des Werkstücks schützen sie auch komplexe Geometrien vor Korrosion.
Die Korrosionsbeständigkeit verbessert sich mit zunehmender Dicke der NIPLATE® Beschichtung, wodurch die intrinsische Porosität der Beschichtung verringert wird. Auf der Oberfläche können jedoch durch verschiedene Ursachen wie grobe Porosität des Grundmaterials, nichtmetallische Einschlüsse in der Legierung, Risse in der Beschichtung oder Schäden durch Manipulation oder mechanische Bearbeitung Unregelmäßigkeiten auftreten. Dies kann das Grundmetall der aggressiven Wirkung der äußeren Umgebung aussetzen und Korrosionsstellen auslösen.
Die Beschichtungen aus chemischem Nickel mit hohem Phosphorgehalt NIPLATE® 500 und NIPLATE® eXtremeweisen auch bei geringen Dicken eine sehr geringe Porosität auf. In der Regel weisen diese Beschichtungen mit einer Dicke von mehr als 30 µm keine Porosität auf.
Schutz von Kupferlegierungen
Bei Kupferlegierungen ist der Schutzmechanismus anders. Kupfer hat ein größeres Redoxpotenzial als Nickel, daher erzeugt die chemische Nickelbeschichtung auch einen kathodischen Schutz des Grundmaterials. Dies führt zu einer außergewöhnlichen Korrosionsbeständigkeit von mit NIPLATE® beschichteten Kupferlegierungen, auch bei Beschädigung und Diskontinuität der Beschichtung.
Dies bedeutet, dass Kupferlegierungen, die mit chemisch vernickelten Beschichtungen behandelt wurden, auch bei direktem Kontakt zwischen Meerwasser und behandelten Teilen in Meeresumgebungen verwendet werden können.
PRAKTISCHE TIPPS
- Kupferlegierungen: Sie sind das Grundmaterial, das durch die NIPLATE® Beschichtungen am besten vor Korrosion geschützt ist.
- Aluminium- oder Kohlenstoffstahllegierungen: Für Anwendungen, bei denen die Korrosionsbeständigkeit von entscheidender Bedeutung ist, sollte eine Beschichtungsdicke von mindestens 20 µm auf Aluminium- oder Kohlenstoffstahllegierungen vorgesehen werden.
- Qualität und mechanische Verarbeitung: Um die Korrosionsbeständigkeit zu maximieren, ist es ratsam, ein hochwertiges Rohmaterial zu verwenden, das frei von Porosität oder Einschlüssen ist. Es ist auch notwendig, eine feine mechanische Bearbeitung mit geringer Rauheit durchzuführen, alle Grate oder scharfen Kanten zu entfernen und im Falle der Verwendung von nicht emulgierbaren Ölen während der mechanischen Bearbeitung eine Lösungsmittelwäsche der Teile unmittelbar nach der Verarbeitung durchzuführen.
Beschleunigte Korrosionsbeständigkeitsprüfung bei neutralem Salznebel
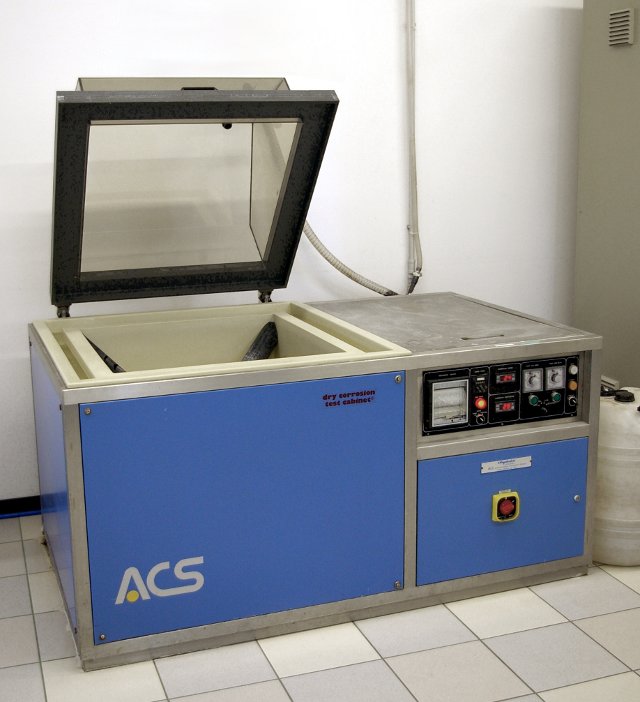
Der am häufigsten verwendete Korrosionsbeständigkeitstest in der mechanischen Industrie ist der beschleunigte Korrosionsbeständigkeitstest bei neutralem Salznebel ISO 9227.
Das bedeutet, dass das Werkstück einem Nebel aus Wasser und Salz (5 % Natriumchlorid) bei einer Temperatur von 35 °C für eine Zeit ausgesetzt wird, die normalerweise zwischen 96 und 480 Stunden liegt und so eine extrem korrosive Umgebung für viele Materialien schafft.
Ein grundlegender Schritt für die Bewertung und Definition der Festigkeit ist die Messung der korrodierten Fläche. Durch diese Maßnahme wird das Schutzrating Rp nach ISO 10289 berechnet.
NIPLATE® Beschichtungen
Die NIPLATE® Beschichtungen bieten eine hohe chemische Beständigkeit gegen diese korrosive Umgebung und sind fast vollständig korrosionsbeständig. Der Korrosionsschutz erfolgt durch Isolierung des Grundmaterials von der Umgebung; daher wird jede Diskontinuität/Unregelmäßigkeit der Beschichtung zu einer potenziellen Angriffszone.
Korrosionsbeständigkeit von Eisen- und Aluminiumlegierungen
Die Korrosionsbeständigkeit von beschichteten Eisen- und Aluminiumlegierungen im Salznebel hängt von der Beschichtung, der mechanischen Bearbeitung und vom Grundmaterial des Werkstücks ab. Angesichts der vielen beteiligten Parameter erfordert eine Definition der Korrosionsbeständigkeit notwendigerweise die Durchführung eines Salzsprühtests am beschichteten Werkstück.
Korrosionsbeständigkeit von Kupferlegierungen
Das Verhalten von mit NIPLATE® beschichteten Kupferlegierungen bei einem Salzsprühnebeltest ist unterschiedlich. Dank der elektrochemischen Affinität zwischen Nickel und Kupfer ist der Korrosionsschutz auch bei geringen Beschichtungsdicken bemerkenswert. Ein mit einer Dicke von 30 µm NIPLATE® 500 beschichtetes Messingstück weist eine Korrosionsbeständigkeit im Salznebel mit einer Bewertung von Rp 9 auf, auch bei einer Exposition von mehr als 1000 Stunden.
Schlussfolgerungen
Diese Eigenschaften machen die NIPLATE® Beschichtungen besonders geeignet für eine Vielzahl von industriellen Anwendungen. Die Korrosionsbeständigkeit, die durch den Salzsprühtest bestimmt wird, trägt wesentlich zur Verlängerung der Lebensdauer der Teile bei und gewährleistet eine wirksame Barriere gegen Korrosionsmittel. Die technischen Spezifikationen und die Art der Anwendung der NIPLATE® Beschichtungen sollten immer durch Feldtests unter Berücksichtigung der Komplexität und Vielfalt der Betriebsbedingungen überprüft werden.