Eigenschaften der chemischen Vernickelung
Härte und Verschleißfestigkeit
Härte
Die NIPLATE® Beschichtungen besitzen eine deutlich höhere Härte als die typischerweise beschichteten Substrate, was dazu beiträgt, ihre tribologischen Eigenschaften zu erhöhen. Im Vergleich zu herkömmlichen und kommerziell vergleichbaren Beschichtungen (wie elektrolytische Vernickelung, anodische Oxidation von Aluminium und thermochemische Behandlungen von Stählen) weisen sie eine durchschnittlich höhere Härte auf, die mit der von Hartchrombeschichtungen vergleichbar ist.
Es ist jedoch zu beachten, dass die Härte des chemischen Nickels geringer ist als bei speziellen Beschichtungen wie Plasma-Spray, PVD/CVD, die jedoch erhebliche Unterschiede in Bezug auf Kosten und Anwendung aufweisen.
In der folgenden Tabelle sind die Härten der Beschichtungen zusammengefasst, die in Bezug auf die durchgeführten Wärmebehandlungen erhalten werden können:
Härte [HV] | Dehydrierung 150-180 °C für 4 Std. | Aushärtung 260-280 °C für 8 Stunden | Aushärtung 330-350 °C für 4 Std. |
---|---|---|---|
NIPLATE® 500 | 550 ± 50 HV | - | 1000 ± 50 HV |
NIPLATE® 600 | 700 ± 50 HV | 800 ± 50 HV | 1000 ± 50 HV |
NIPLATE® 500 PTFE | 250 ± 100 HV | 300 ± 100 HV | - |
NIPLATE® 600 SiC | 700 ± 50 HV | 850 ± 50 HV | 1050 ± 50 HV |
PRAKTISCHE TIPPS
Die maximale Härte der NIPLATE® Beschichtungen kann durch eine Aushärtungsbehandlung bei 340 °C für 4 Stunden erreicht werden. Dieser Prozess führt zu einer schillernden gelb-blauen Färbung der Beschichtung. Bei Bedarf kann eine Wärmebehandlung zur Härtung in inerter Atmosphäre durchgeführt werden. Diese Methode ermöglicht es, die maximale Härte der Beschichtung zu erreichen, wobei die metallisch-weiße Färbung des chemischen Nickels unverändert bleibt.
Verschleißfestigkeit
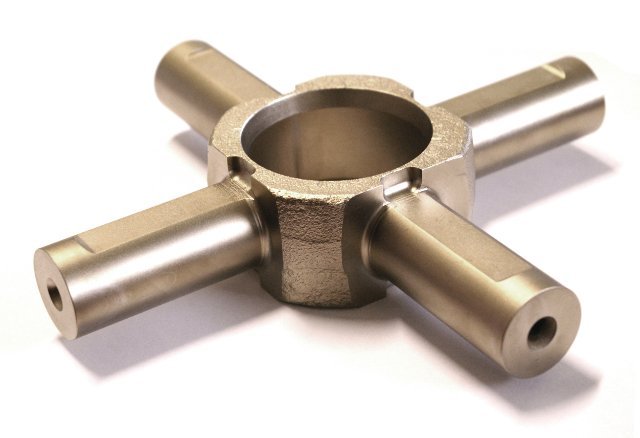
Dank ihrer Härte und Kohäsion ermöglichen die NIPLATE® Beschichtungen, insbesondere NIPLATE® 600 und NIPLATE® 600 SiC, eine hohe Verschleißfestigkeit der behandelten Oberflächen.
NIPLATE® 600, mit einem 7-prozentigen-Phosphorgehalt der Legierung, bietet eine hohe Beständigkeit gegen abrasiven Verschleiß, Haftverschleiß und Fretting, sowohl in geschmierter als auch in trockener Umgebung. Die mit den Wärmebehandlungen erreichte Härte und die erzielbaren hohen Beschichtungsdicken (bis zu 50-70 µm) ermöglichen es, die Lebensdauer des Bauteils zu erhöhen und eine ähnliche Verschleißfestigkeit wie Hartchrom zu erzielen, mit dem Vorteil, dass das Werkstück nicht nachgeschliffen werden muss und eine gleichmäßige Beschichtungsdicke auf der gesamten Oberfläche, sowohl innen als auch außen, vorhanden ist.
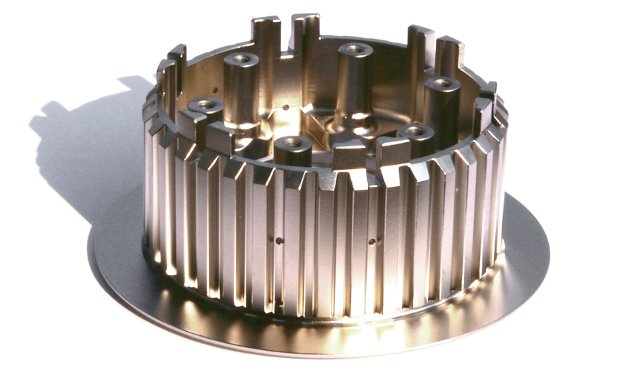
Für kritische Anwendungen, bei denen der Verschleiß des Bauteils maximal ist, wurde NIPLATE® 600 SiC entworfen, eine Matrix-Verbundbeschichtung NIPLATE® 600, die mikrokristalline Körner aus Siliciumcarbid in einer Menge von 20-30 Volumenprozent enthält. Die Partikel aus Siliciumcarbid, einem ultraharten synthetischen Keramikmaterial, ermöglichen eine Beschichtung mit außergewöhnlichen Verschleißfestigkeitseigenschaften. Die Abriebfestigkeit von NIPLATE® 600 SiC ist bis zu 10-mal höher als die von Hartchrom. Diese Beschichtung wird in hochtechnologischen Bereichen eingesetzt, beispielsweise im Rennsport, um die Leistung zu erhöhen, ohne die Lebensdauer der Teile zu verringern, oder in Textilien, um die Teile zu schützen, die einem ständigen Verschleiß des Webfadens unterliegen.
PRAKTISCHE TIPPS
- Für Bauteile, die einem starken Verschleiß unterliegen, ist eine Behandlungsdicke von mindestens 20 µm und eine anschließende Aushärtungsbehandlung bei 280 °C für 8 Stunden oder besser noch bei 340 °C für 4 Stunden geeignet.
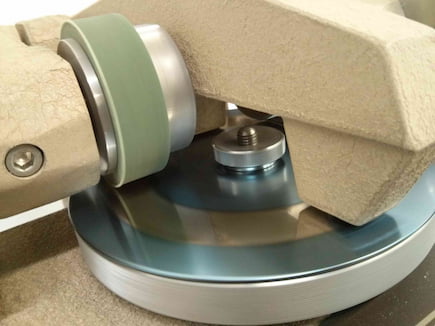
Taber-Abraser-Abriebtest
Der am häufigsten verwendete Test zur Messung der Abriebfestigkeit von Beschichtungen ist der Taber-Abraser-Abriebtest. Der Verschleißtest für chemische Nickelbeschichtungen ist in der amerikanischen Norm ASTM B733 festgelegt. Die Prüfparameter lauten wie folgt:
- Schleifräder: CS-10
- Einzelradlast: 1000 g
- Höhe der Saugdüsen: 1 mm
Die Prüfung wird durchgeführt, indem die Proben auf eine rotierende Platte montiert werden, wobei sie unter Anwendung einer bestimmten Kraft zwei abrasiven Rädern ausgesetzt werden, die rollen und gleichzeitig reiben. Die Verschleißrückstände während der Prüfung werden über zwei Düsen angesaugt, die sich über dem Prüfling befinden. Am Ende des Verschleißtests wird der Taber Wear Index (TWI) berechnet, ein Index des Verschleißes der Beschichtung, der als durchschnittliche Gewichtsänderung in mg über 1000 Zyklen berechnet wird.
Die folgende Tabelle zeigt die TWI-Werte der NIPLATE® Beschichtungen. Ein niedriger Wert weist auf eine höhere Abriebfestigkeit hin.
Verschleißfestigkeit [TWI] | Dehydrierung – 150-180 °C für 4 Std. | Aushärtung – 260-280 °C für 8 Stunden | Aushärtung – 330-350 °C für 4 Std. |
---|---|---|---|
NIPLATE® 500 | 20 TWI | - | 10 TWI |
NIPLATE® 600 | 16 TWI | 12 TWI | 9 TWI |
NIPLATE® 500 PTFE | 33 TWI | 19 TWI | - |
NIPLATE® 600 SiC | 0,70 TWI | 0,65 TWI | 0,60 TWI |