Introduction
NIPLATEĀ® Coatings
Traditional Niplate coatings
The electroless nickel plating process uses sodium hypophosphite, a reducing agent that transforms nickel ions into nickel metal on the surface of the object to be coated. During the reaction, an alloy of nickel and phosphorus is also deposited.
Electroless nickel plating coatings are divided according to their phosphorus content:
- NIPLATEĀ® 600: Medium Phosphorus 5%ā9% P
- NIPLATEĀ® 500 and NIPLATEĀ® eXtreme: High Phosphorus 10%ā13% P
Both types have the following characteristics:
- Can coat almost any metal alloy
- Even and uniform thickness
- Coating thickness from 3 to 50 µm
The main differences lie in their wear and chemical resistance. For example:
- NIPLATEĀ® 600 should be chosen when needing greater resistance to wear.
- NIPLATEĀ® 500 and NIPLATEĀ® eXtreme should be chosen when needing high chemical and corrosion resistance.
Technical specifications
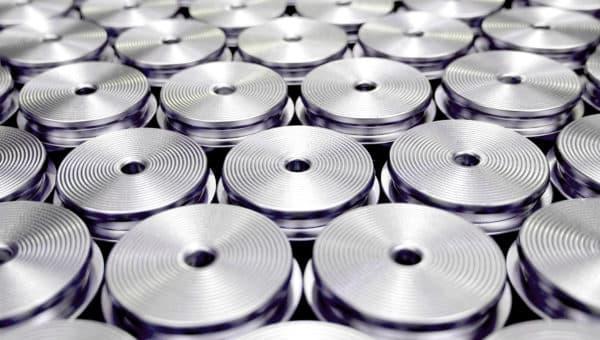
NIPLATEĀ® 600 ā Medium Phosphorus Electroless Nickel Plating
Wear resistance | Corrosion resistance | ISO 4527 NiP(7)
NIPLATEĀ® 600 is a medium phosphorus (5ā9% in P) electroless nickel plating coating. NIPLATEĀ® 600 is the most widely used of the Niplate electroless nickel coatings thanks to its high wear resistance, good corrosion resistance, and low cost.
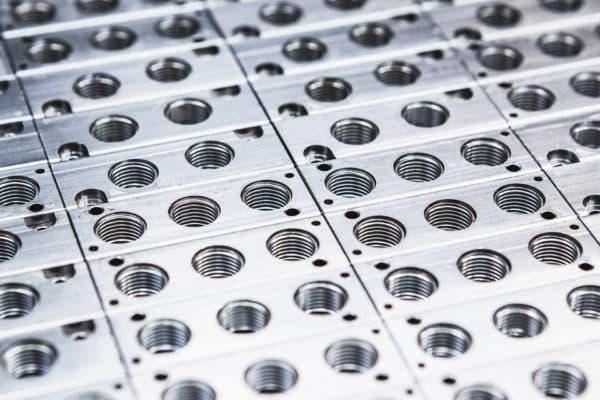
NIPLATEĀ® 500 ā High Phosphorus Electroless Nickel Plating
Wear resistance | Corrosion resistance | ISO 4527 NiP(11)
NIPLATEĀ® 500 is a high-phosphorus (10ā13% in P) electroless nickel plating. Niplate 500 should be chosen over other Niplate coatings when components will be in contact with food and when high corrosion resistance and protection from harsh chemicals are required.
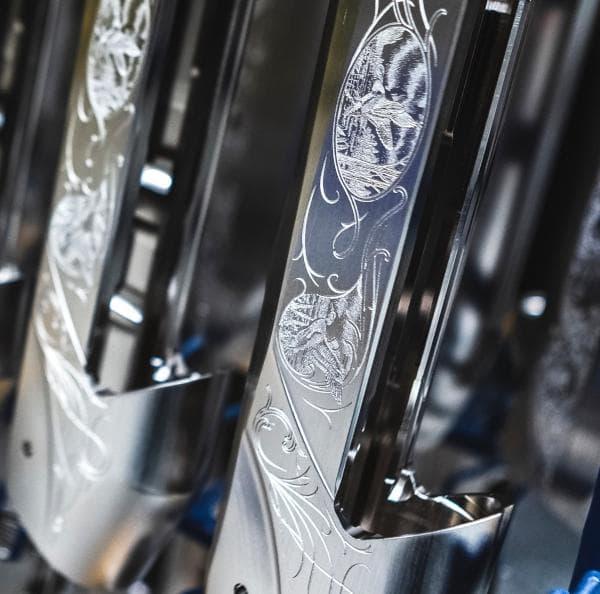
NIPLATE Ā® eXtreme Electroless nickel plating
Excellent corrosion resistance, especially on aluminum
Niplate Ā® eXtreme is an electroless nickel plating specifically developed for increased corrosion resistance, especially on aluminum alloys. It can be applied on all aluminum alloys, both machined and cast alloys.
Composite Niplate coatings
Composite coatings are developed to improve the surface properties of electroless nickel plating. Particles with specific properties are co-deposited, such as:
- Niplate 500 PTFE: Contains 25ā35% PTFE particles, providing a low coefficient of friction and non-stick properties.
- Niplate 600 SiC: Contains 20ā30% silicon carbide (SiC) particles, providing exceptional wear resistance.
Technical specifications
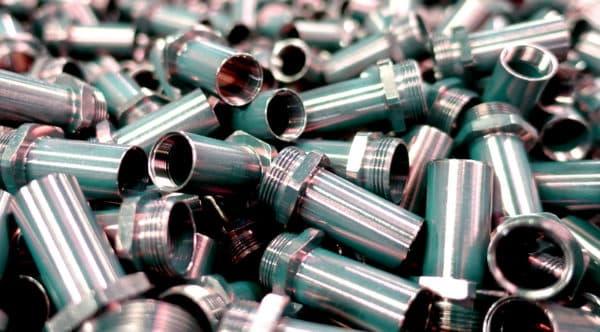
NIPLATEĀ® 500 PTFE Electroless Nickel Plating with PTFE
Self-lubricating | Non-stick
NiplateĀ® 500 PTFE is a composite coating of high phosphorus (10ā13%) electroless nickel plating containing 25ā35% PTFE particles. The coating has a very low coefficient of friction (0.08ā0.10), non-stick properties and excellent adhesion to the substrate metal.
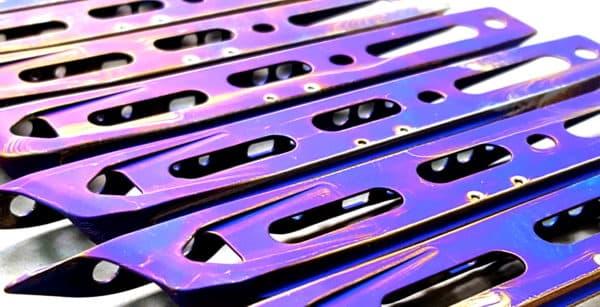
NIPLATEĀ® 600 SiC Electroless Nickel Plating with SiC
Extreme wear resistance
NiplateĀ® 600 SiC is a composite coating of medium phosphorus (5ā9%) electroless nickel plating and 20ā30% silicon carbide (SiC) particles. The coating is used for applications in which resistance to abrasive and adhesive wear is of paramount importance.