Electroless plating properties
Corrosion resistance
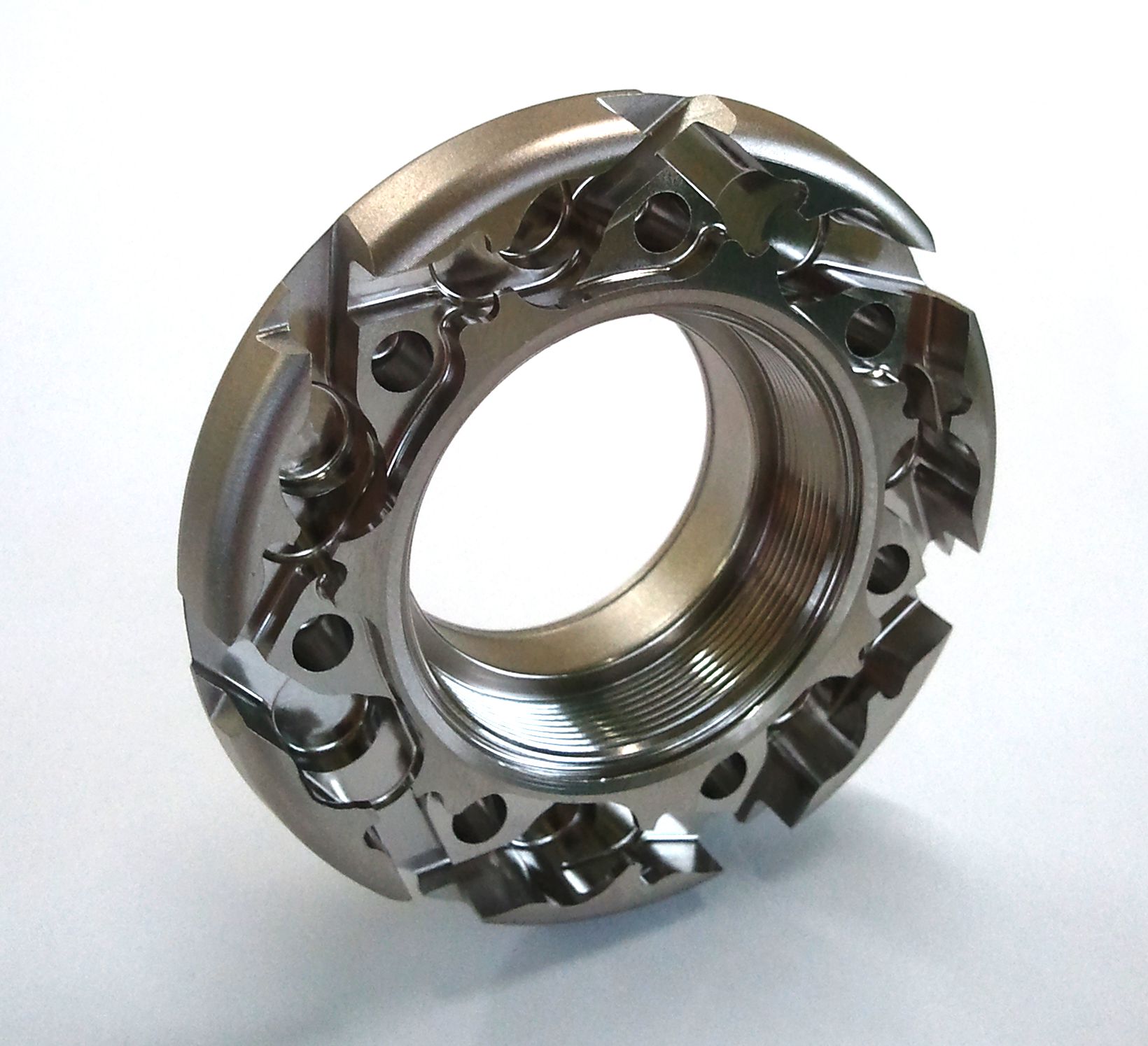
One of the most salient properties of NIPLATE® coatings is their corrosion resistance. These coatings are composed of a nickel and phosphorus alloy, presenting high chemical resistance in environments that are typically harsh on common metal alloys, such as marine, industrial, and road environments. Furthermore, Niplate coatings are not susceptible to chemical assault by hydrocarbons and solvents.
Protection Mechanism
The corrosion protection mechanism of NIPLATE® coatings occurs by isolating the base material from the corrosive environment. Thanks to their uniformity over the entire surface of the workpiece, they protect even complex geometries from corrosion.
Corrosion resistance improves with increased thickness of the NIPLATE® coating, reducing its intrinsic porosity. However, discontinuity points may exist on the surface, due to a variety of causes such as coarse porosity of the base material, non-metallic inclusions in the alloy, coating cracks, or damage due to handling or machining. This can expose the base metal to the harsh action of the external environment, triggering corrosion spots.
High phosphorus NIPLATE® 500 and NIPLATE® eXtreme electroless nickel coatings have very low porosity even at low thicknesses. Usually, these coatings have zero porosity at thicknesses greater than 30µm.
Copper Alloy Protection
For copper alloys, the protection mechanism is different. Copper has a higher oxide-reduction potential than nickel, so electroless nickel plating also creates cathodic protection of the base material. This results in exceptional corrosion resistance for copper alloys coated with NIPLATE®, even when there is damage and discontinuity in the coating.
This means that copper alloys treated with electroless nickel plating coatings can be used in marine environments even when there is direct contact between seawater and the treated parts.
PRACTICAL RECOMMENDATIONS
- Copper Alloys: They are the base material that is best protected from corrosion with NIPLATE® coatings.
- Aluminum or Carbon Steel Alloys: For applications where corrosion resistance is critical, a coating thickness of at least 20 µm should be stipulated for aluminum or carbon steel alloys.
- Quality and Machining: To maximize corrosion resistance, a high-quality raw material free of porosity or inclusions should be used. It is also necessary to carry out fine machining with low roughness, remove any burrs or sharp edges and, if non-emulsifiable oils are used during machining, solvent wash the workpieces immediately after machining.
Accelerated corrosion resistance test in neutral salt spray
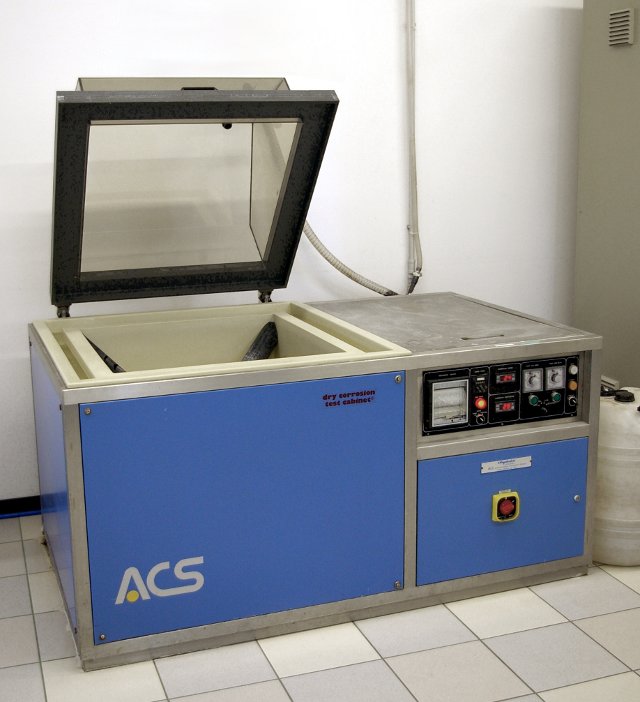
The most commonly used corrosion resistance test in the mechanical industry is the ISO 9227 neutral salt spray accelerated corrosion resistance test.
It involves exposing the workpiece to a mist of water and salt (5% sodium chloride) at a temperature of 35°C for a time usually varying between 96 or 480 hours, creating an extremely corrosive environment for many materials.
A fundamental step for resistance evaluation and definition is the measurement of the corroded area. Using this measure, the Rp protection rating is calculated according to the ISO 10289 standard.
NIPLATE® coatings
NIPLATE® coatings provide high chemical resistance to this corrosive environment and are almost completely immune to corrosion. Corrosion protection occurs by isolating the base material from the environment; therefore, any discontinuity in the coating becomes a potential attack zone.
Corrosion Resistance of Iron and Aluminum Alloys
Salt spray corrosion resistance of coated iron and aluminum alloys depends on the coating, machining, and base material of the workpiece. Considering the numerous parameters involved, defining corrosion resistance necessarily requires the execution of the salt spray test on the coated workpiece.
Corrosion Resistance of Copper Alloys
The salt spray corrosion test behavior of copper alloys coated with NIPLATE® is different. Thanks to the electrochemical affinity between nickel and copper, corrosion protection is remarkable even with low coating thicknesses. A piece of brass coated with 30 µm of NIPLATE® 500 has a salt spray corrosion resistance rating of 9 Rp, even for exposure exceeding 1000 hours.
Conclusions
These properties make NIPLATE® coatings particularly suitable for a wide range of industrial applications. Corrosion resistance, determined through the salt spray test, significantly contributes to extending the useful life of components, ensuring an effective barrier against corrosive agents. The technical specifications and application methods of NIPLATE® coatings should always be verified by field testing, considering the complexity and variety of operating conditions.