Electroless plating properties
Hardness and Wear Resistance
Hardness
NIPLATE® coatings have a considerably higher hardness than that of typically coated substrates, and this contributes to their increased tribological properties. Compared to traditional and commercially comparable coatings (such as nickel electroplating, anodic aluminum oxidation, and steel thermochemical treatments), they exhibit a higher average hardness, comparable to that of hard chrome coatings.
Nevertheless, it should be noted that the hardness of electroless nickel plating is lower than specialized coatings, such as PVD/CVD plasma sprays, which, however, have considerable differences in terms of cost and application.
The table below summarizes the coating hardnesses that can be obtained in relation to the heat treatments performed:
Hardness [HV] | Dehydrogenation 150–180°C for 4h | Hardening 260–280°C for 8h | Hardening 330–350°C for 4h |
---|---|---|---|
NIPLATE® 500 | 550 ± 50 HV | - | 1000 ± 50 HV |
NIPLATE® 600 | 700 ± 50 HV | 800 ± 50 HV | 1000 ± 50 HV |
NIPLATE® 500 PTFE | 250 ± 100 HV | 300 ± 100 HV | - |
NIPLATE® 600 SiC | 700 ± 50 HV | 850 ± 50 HV | 1050 ± 50 HV |
PRACTICAL RECOMMENDATIONS
The maximum hardness of NIPLATE® coatings can be obtained using a hardening treatment at 340°C for 4 hours. This process causes the coating to become iridescent yellow-blue in color. If necessary, a hardening heat treatment can be performed in an inert atmosphere. This method achieves maximum coating hardness while maintaining the electroless nickel plating's metallic white color.
Wear Resistance
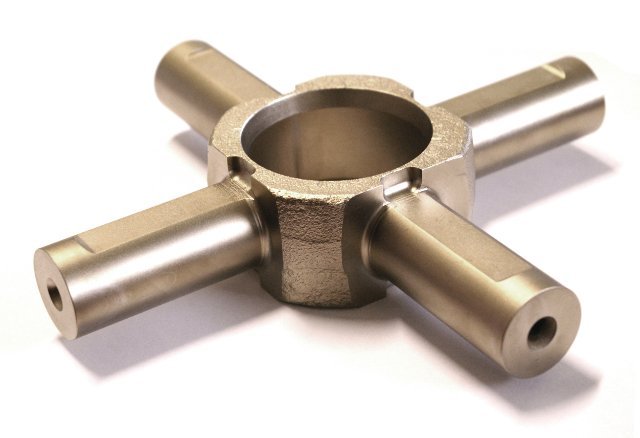
Thanks to their hardness and cohesion, NIPLATE® coatings — in particular NIPLATE® 600 and NIPLATE® 600 SiC — make it possible to obtain high wear resistance on treated surfaces.
With a 7% phosphorus alloy content, the NIPLATE® 600 coating provides high resistance to abrasive wear, adhesive wear, and fretting, in both lubricated and dry environments. The hardness achieved with hardening heat treatments and the high coating thicknesses that can be obtained (up to 50–70 µm) make it possible to increase the component's lifespan and achieve wear resistance similar to hard chrome, with the advantage of not having to subsequently grind the workpiece and having a uniform coating thickness over the entire surface, both internal and external.
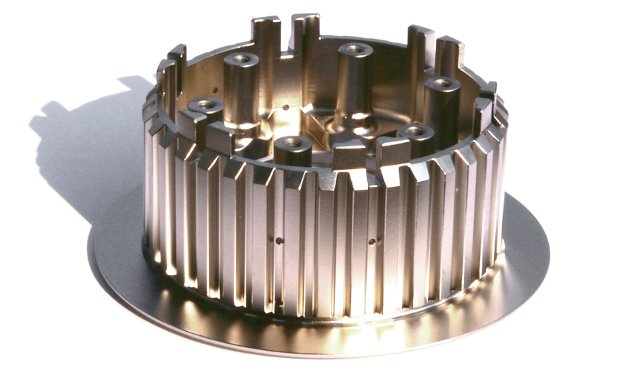
For critical applications, where component wear is highest, NIPLATE® 600 SiC — a NIPLATE® 600 matrix composite coating containing micro-crystalline grains of silicon carbide in amounts of 20–30% by volume — has been developed. An ultra-hard synthetic ceramic material, silicon carbide particles make it possible to obtain a coating with extraordinary wear resistance properties. The abrasive wear resistance of NIPLATE® 600 SiC is up to 10 times greater than that of hard chrome. This coating is used in high-tech industries such as racing, to increase performance without decreasing component life, or in textiles, to protect components subject to the constant wear and tear of weaving threads.
PRACTICAL RECOMMENDATIONS
- For components subject to heavy wear, include a treatment thickness of at least 20 µm with a subsequent hardening treatment at 280°C for 8 hours or, better still, at 340°C for 4 hours.
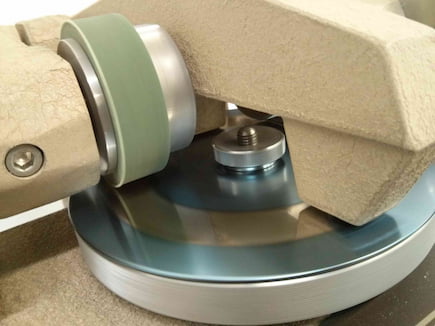
Taber Abraser abrasive wear test
The most widely used test for measuring abrasive wear resistance on coatings is the Taber Abraser Test. The wear test on electroless nickel coatings is specified by the American standard ASTM B733. The test parameters are as follows:
- Abrasive wheels: CS-10
- Load on single wheel: 1000 g
- Suction nozzle height: 1 mm
The test is carried out by mounting the specimens on a turntable, subjecting them to the contact of two abrasive wheels that simultaneously roll and rub, applied with a specific force. Wear residues during the test are vacuumed away by means of two nozzles positioned above the specimen. At the end of the wear test, the Taber Wear Index (TWI) is calculated, an index of wear incurred by the coating, calculated as an average change in weight expressed in mg over 1000 cycles.
The following table lists the TWI values of the NIPLATE® coatings. A lower value indicates greater resistance to abrasive wear.
Wear resistance [TWI] | Dehydrogenation - 150–180°C for 4h | Hardening - 260–280°C for 8h | Hardening - 330–350°C for 4h |
---|---|---|---|
NIPLATE® 500 | 20 TWI | - | 10 TWI |
NIPLATE® 600 | 16 TWI | 12 TWI | 9 TWI |
NIPLATE® 500 PTFE | 33 TWI | 19 TWI | - |
NIPLATE® 600 SiC | 0.70 TWI | 0.65 TWI | 0.60 TWI |